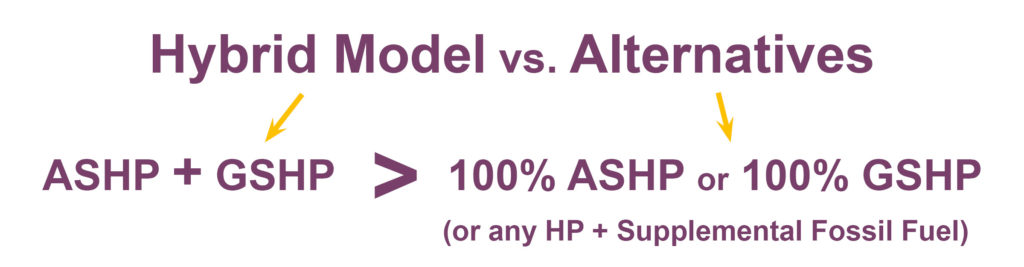
Although uncommon, systems composed of a hybrid, or mix of heat pump technologies are a better solution than any single type of heat pump, or heat pump with a supplemental fossil fuel combustion heat source. Well designed hybrid heat pump systems balance upfront costs with low operating costs, resulting in maximum system efficiency, cost effectiveness, and the potential for net zero emissions.
The market for heat pumps is experiencing strong growth. The growth is propelled by recent advances in technology that make heat pumps efficient over a wider range of input and output temperatures. Also, they also can be used for both heating and cooling; a desirable feature. There are several types of heat pumps, the two main ones being ground source heat pumps (GSHPs) and air source heat pumps (ASHPs). These heat pumps are usually deployed as a single type, or in combination with a fossil fuel heat source. Hybrid heat pump systems are those that use both ASHPs and GSHPs.
Heat pumps are “all electric”. All electric heat pump systems in new buildings will soon be the norm as efficiency, sustainability, and emissions reduction goals are prioritized. This is also true in retrofits of buildings with older heating systems like steam, oil-fired warm air furnaces, and similar gas fired equipment . As power from renewables continues to grow market share, and as fully electric systems have the potential to be dominant market leaders in efficiency, the greenhouse gas emissions footprint of these buildings will be greatly reduced. Appropriately designed heat pump driven heating and cooling systems have the efficiency potential to help achieve net zero emissions goals.
Heat Pump Principles
Heat pumps move heat; from a heat source to a heat sink. For heating applications, the principal energy source, be it sub-surface ground or ambient air, is on site, sustainable, and free. Heat pumps take the freely available thermal energy from the air (ASHPs) and from the ground (GSHPs), and boost it to a higher temperature with a compression/expansion cycle. The process is reversed in summer for cooling by taking heat from inside and expelling it to the air or the ground. Heat pumps are most efficient when the difference in temperature between the source (e.g. air or ground) and the output are close. In winter, as the source temp declines, the system loses efficiency. Likewise, higher output temperatures also lower efficiency.
Leveraging Heat Pump Strengths
Here in New England, the temperature in the ground 6 feet below the surface is a steady (approx.) 55°F year round. During the heating season, removing thermal energy from the ground reduces the ground temperature around the heat exchanger. It’s not unusual for the ground temperature around a geothermal borehole or horizontal loop to drop from 55°F to below 30°F. The ground temperature gets slowly replenished, from moving groundwater for instance, but it doesn’t get back up to its starting temperature until after the heating season is over.
With ground temperatures dropping by 20°F or more, system efficiency can easily drop by 30% or more. So if a stand-alone GSHP system is being designed for high efficiency, more boreholes are required to keep the system efficient. Boreholes are expensive to drill and fit up, and they can’t be located too close together. Also, sizing for 100% of the heat load with GSHPs doesn’t make good sense economically, as the heat load only approaches 100% for a matter of hours or days in the year. The answer is to include another heat source to supplement the GSHPs. As you will see, air source heat pumps make a lot of sense to be that supplemental source of energy.
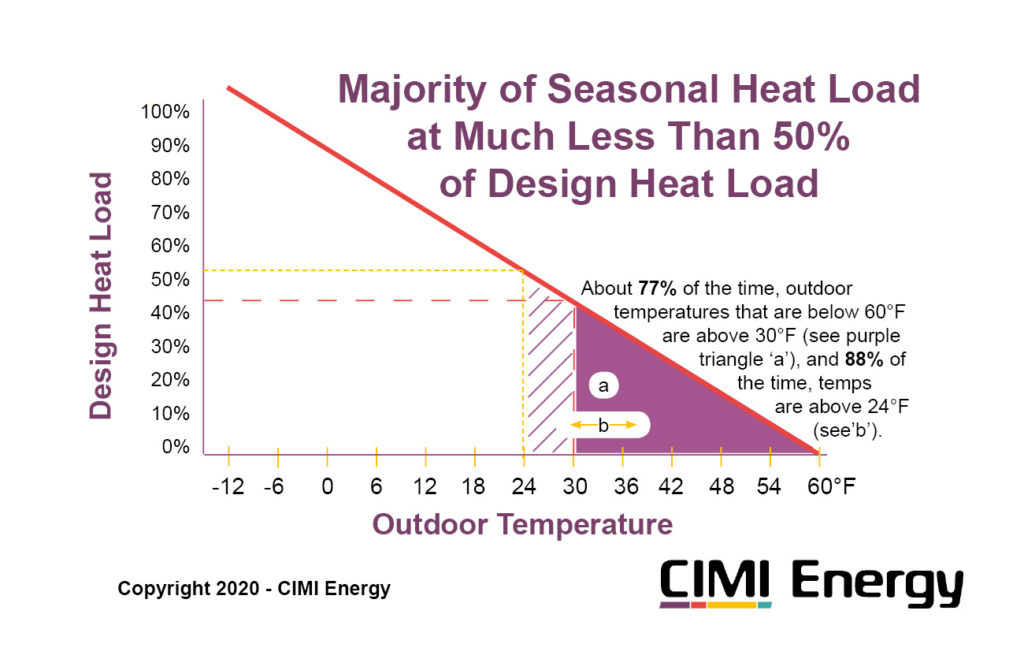
Mixing Heat Pump Types to Make Hybrid Systems
As shown in the image below, most of the time that buildings need heat, the ambient air temperatures are in the 30s, 40s and 50s°F. In eastern Massachusetts, when the temperature is below 60°F, the air temperature is above 30°F for 77% of the time!
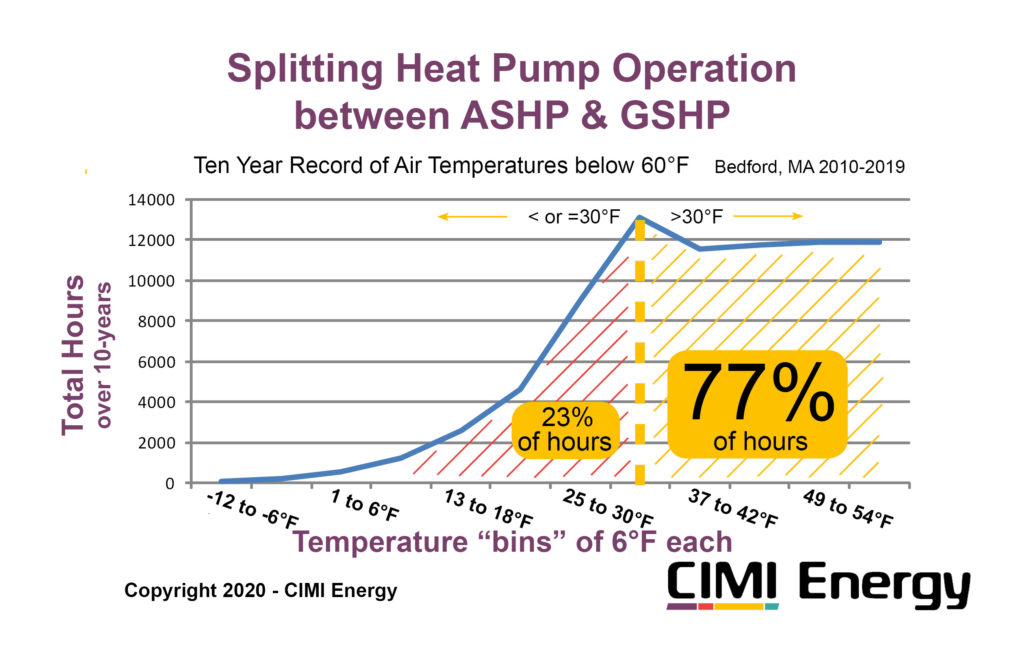
When air temperatures are in the 50s, efficiencies between GSHPs and ASHPs are roughly equivalent because the source temperatures are the same. When outdoor air temperatures are in the 40s, the GSHPs have a marginal efficiency advantage over the ASHPs. The difference in efficiency becomes more significant when temperatures drop to the 30s and below.
It’s worth examining the charts above. Most of the heating season, air temperatures are above 30°F. So if the key objective of running a heating system is optimized seasonal efficiency rather than moment-to-moment efficiency, there is good reason to continue to use ASHPs at these above 30F temps. By not using, or by using the GSHPs only sparingly at these relatively mild temperatures, in-ground temperature remains in the 50s so that the GSHPs can be used very efficiently when air temperatures are frigid.
Planning a Hybrid GSHP ASHP System
The key to implementing an efficient and cost effective heat pump installation is with thorough technical and financial planning up front. A good plan should encompass expected energy use and cost analysis, and include monitoring and performance benchmarking over time. Up front costs for GSHPs is much higher than for ASHPs. And as shown, ASHPs are just as efficient for parts of the year. So the plan needs to identify the right balance of costs and benefits.
A feasibility study and design analysis is the best way to approach this problem. The analysis should include a site evaluation, a building evaluation, and a parametric analysis of data related to u–pfront costs, hardware efficiency estimates, and operating costs. A full design plan should also include system control recommendations for balancing the operation of the hybrid system.
To truly optimize the system performance, tracking and benchmarking must be included. Every site is different, so GSHPs will not operate exactly the same at different sites. System performance data matched with weather data, time-of-day and time-of-season data will help to fine tune the system optimization.
Contact CIMI Energy for information about prioritizing energy investments, and planning for your hybrid heat pump applications. [CIMI Energy uses computer modeling and a range of data (including heat load calculations, building occupancy patterns, hardware costs, installation costs, energy costs, manufacturers efficiency data, etc.) to determine the best system plan.]